Case Study
Staci Americas Goes Lights-Out With Corvus One™, Saving Costs and Space
The Challenges
- Fulfillment Speed: Lost or misplaced inventory disrupted workflow–pickers unable to locate goods, replenishments weren’t on time, and outbound orders delayed
- On-Time In-Full (OTIF) penalties: Delayed orders led to contractual penalties from clients and providers
- Time, Labor, and MHE Costs: Missing pallets took on average 6-8 hours to locate (sometimes up to a full day), disrupting the workflow of up to 20 production employees and leading to unnecessary labor and MHE costs
- Storage Space Utilization: Occupied storage locations were often 20-50% full, preventing current customers from expanding or new customers from being added to the warehouse.
The Corvus Solution
-
Implemented the Corvus One Autonomous Inventory Management System to more accurately and efficiently track and store material for multi-client buildings in Georgia and New Jersey.
-
Inventory Discrepancies Corrected Daily: Scheduled lights-out flights are performed nightly off-shift, ensuring any inventory discrepancies flagged by the Corvus One system are corrected pre-shift the next morning, allowing production and inbound teams to focus on their tasks without having to search for inventory.
What Staci Says
Being able to run inventory checks 24/7 without operator assistance has been a game changer. The lights-out capability in the Corvus One system allows our inventory teams to correct discrepancies off-shift and pre-shift before production starts each day; limiting fulfillment delays and production impacts.
Austin Feagins
Senior Director of Transformation & Solution Design
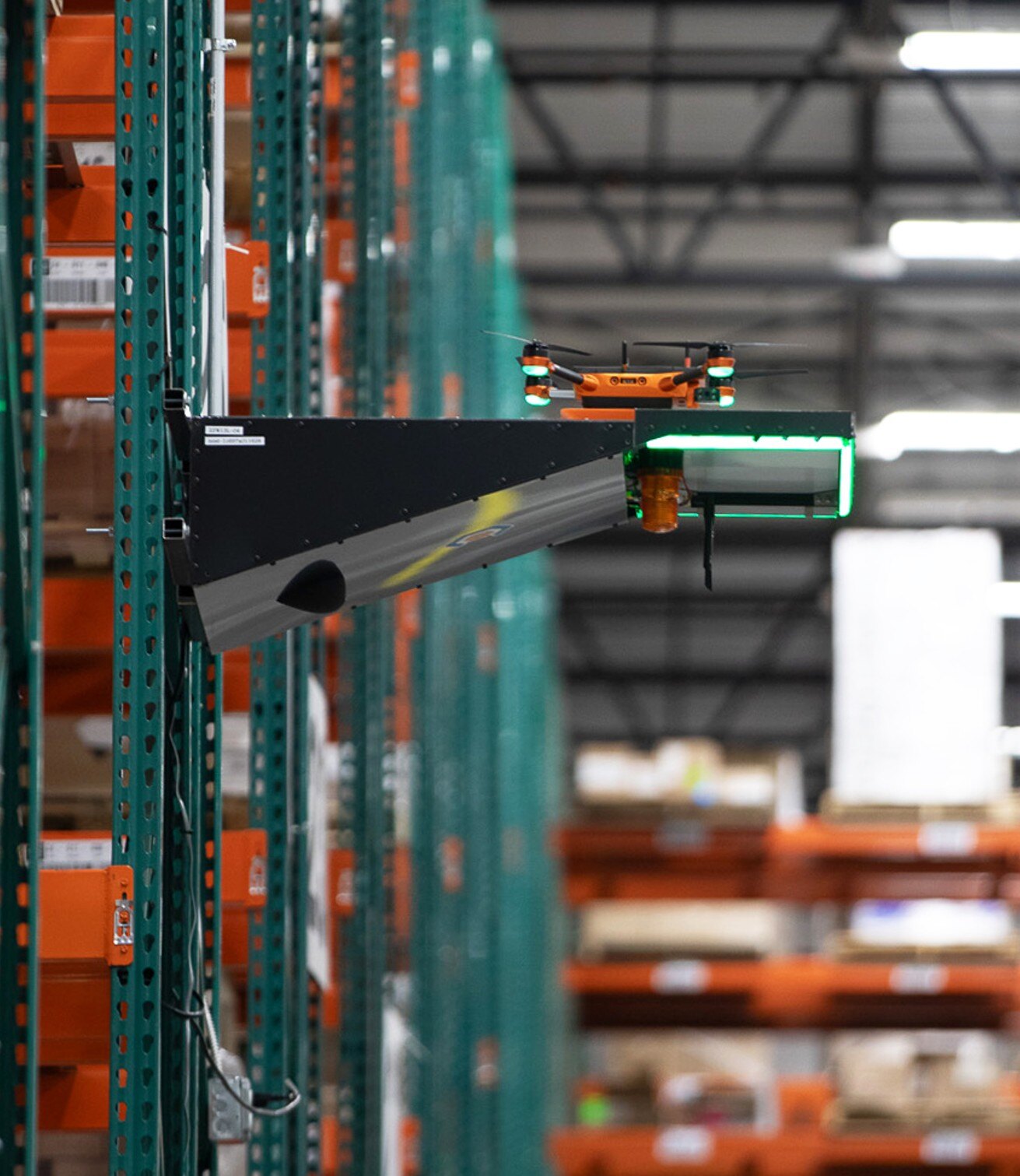
Corvus One warehouse drones autonomously take off and land, charge, and transfer data on premise at the landing pad.
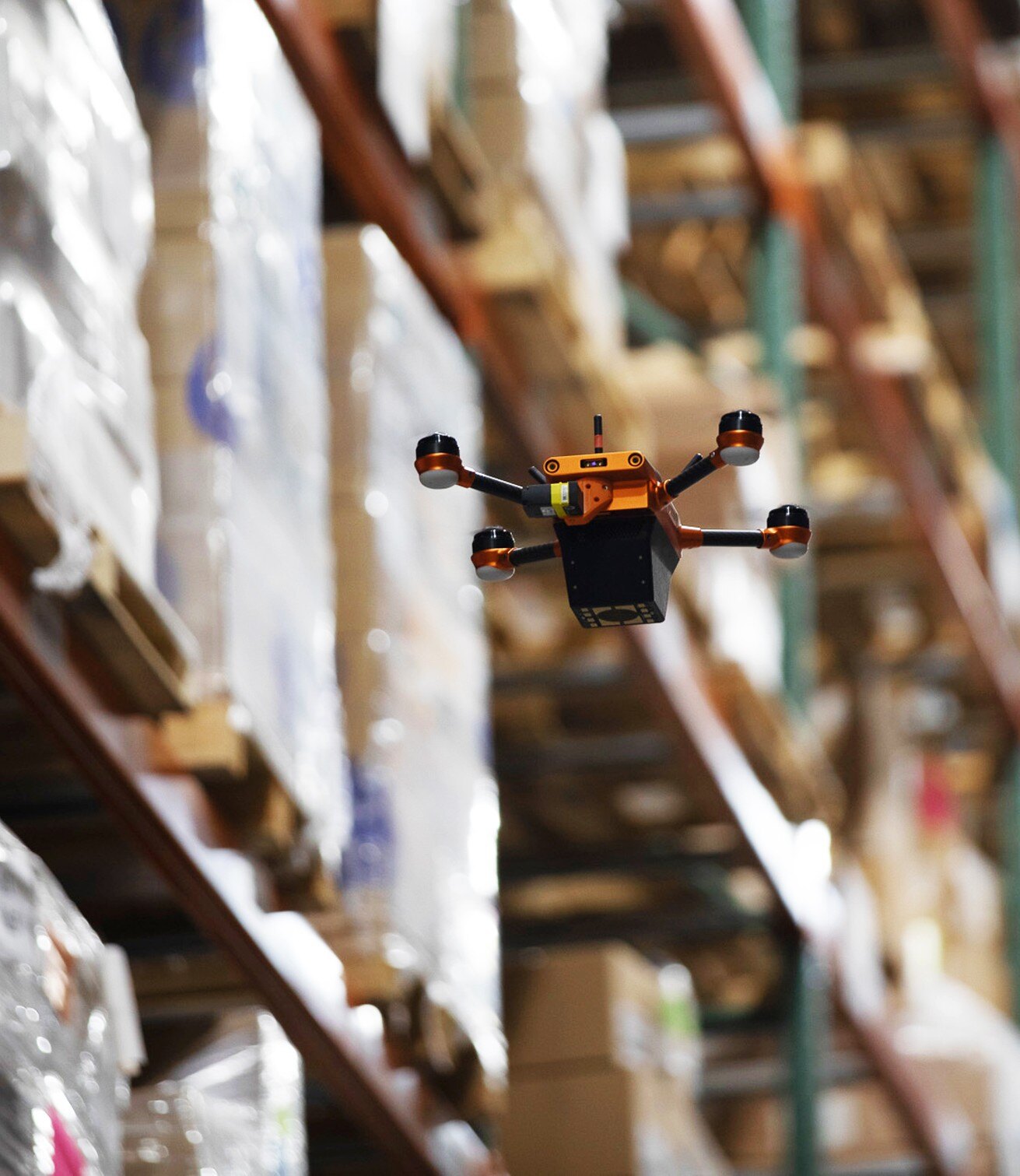
Real-time inventory visibility helps Staci optimize storage locations while helping prevent fulfillment and production delays.
The Impact
- Minimized OTIF penalties: Improved fulfillment speed while significantly reduced contractual penalties for delayed shipments
- Increased Labor Productivity: Production and inbound teams no longer spend time searching for inventory, eliminating unproductive labor and time costs
- Lowered Auditing & Cycle Counting Labor Costs: Skilled employees redeployed to other departments
- Reduced MHE Equipment Usage: Fewer forklifts and cherry pickers needed for operations, lowering equipment costs and reducing emissions
- Improved Space Utilization: Consolidated pallet positions, passing cost savings to customers while opening up more storage space for client expansion or new business
Where Are We Now?
I want them in every single building that we have. We probably have four or five buildings where an urgent deployment makes sense, and our plan is to have them in every one of our U.S. markets in 2025.
Austin F.
Senior Director of Transformation & Solution Design
Drop Us a Line
-
Staci Americas is a third-party logistics (3PL) provider whose services include warehousing, order fulfillment, transportation and returns management. The company is part of Staci Group, a European omnichannel fulfillment provider and bpostgroup company with 78 facilities across the U.S., seven European countries and Asia.
Insights & Resources
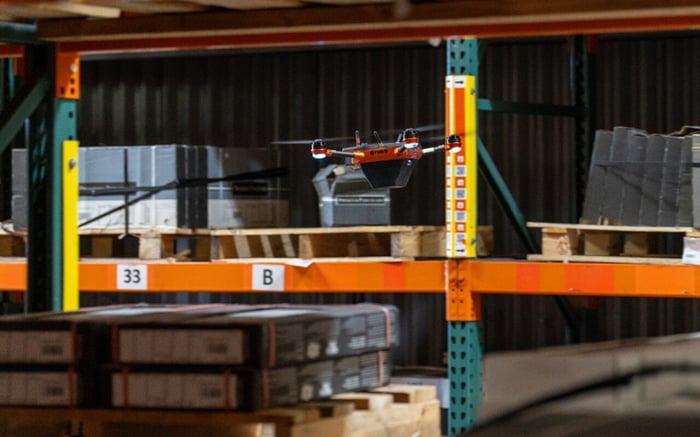
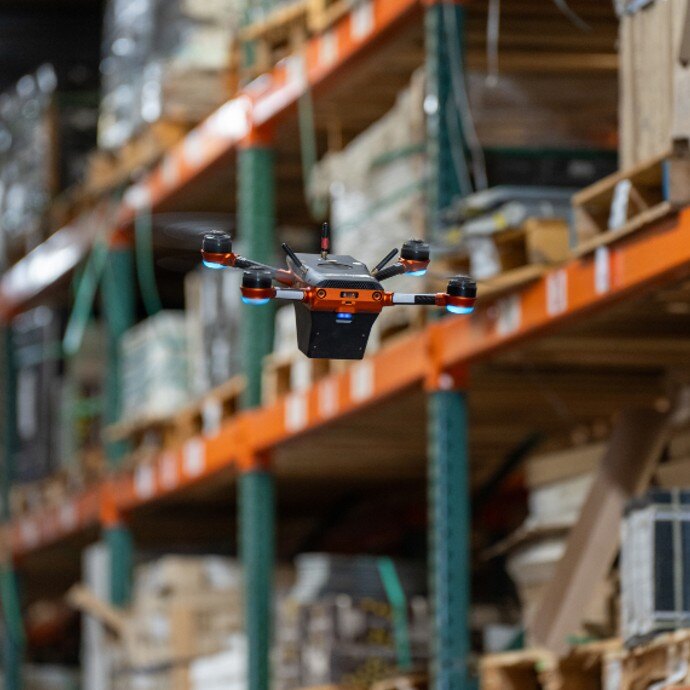
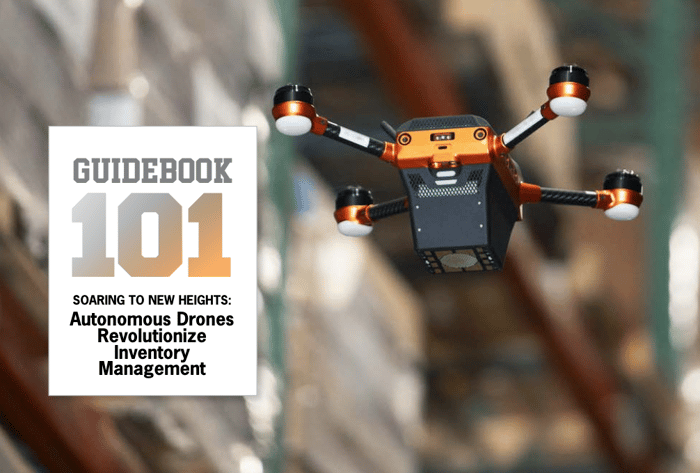