Case Study
MSI Boosts Inventory Management with Corvus One™ Warehouse Drones
Faster Cycle Counting
Labor Reallocation
Recovered Lost Inventory
Inventory Accuracy
The Challenges
-
Fulfillment speed: Lost or misplaced inventory delayed customer deliveries, causing dissatisfaction, returns, and unmet expectations.
-
Inefficient use of labor: Dedicated 2-4 warehouse associates to manually scan inventory for auditing.
-
Productivity: Labor pulled from fulfillment tasks to locate material or vice versa, impacting operational productivity.
The Corvus Solution
-
Implemented the Corvus One™ Autonomous Inventory Management System to more accurately and efficiently track material across MSI's four national distribution centers.
-
No more yearly, wall-to-wall physical inventory checks: the Corvus One™ inventory drones perform daily cycle counting flights, providing MSI with accurate, real-time inventory data.
-
Labor Reallocation: Associates no longer need to perform cycle counts, or search for missing material. Now dedicated to picking and replenishment.
We used to dedicate labor resources to do inventory audits. Now we have drones, which saves us a ton of time and allows us to reallocate our resources to more value-adding tasks like picking or replenishment.
Reggy S.
SVP, Operations
.png?width=1280&height=720&name=Before%20Corvus%20One%20(2).png)
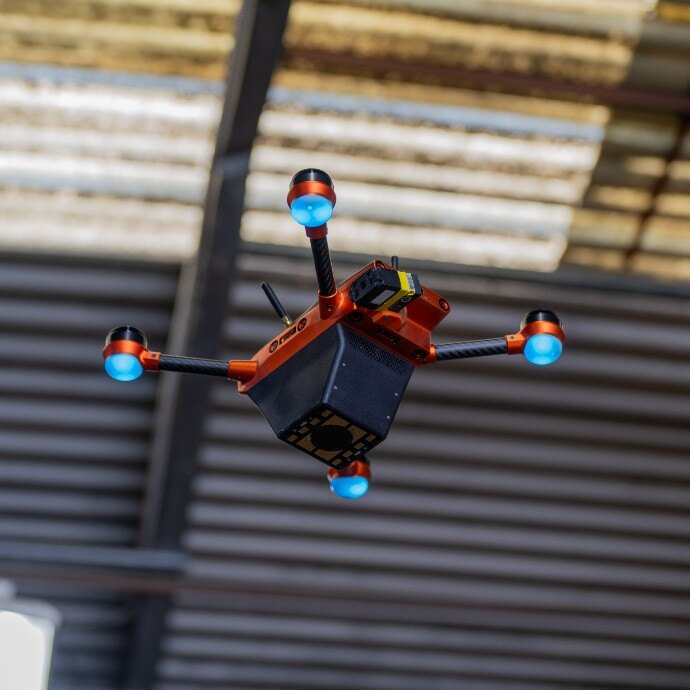
Equipped with obstacle detection, MSI has missions scheduled during operating hours without disrupting workflow or blocking aisles. Corvus One™ warehouse drones fly fully autonomously without reflectors, associates, or Wi-Fi.
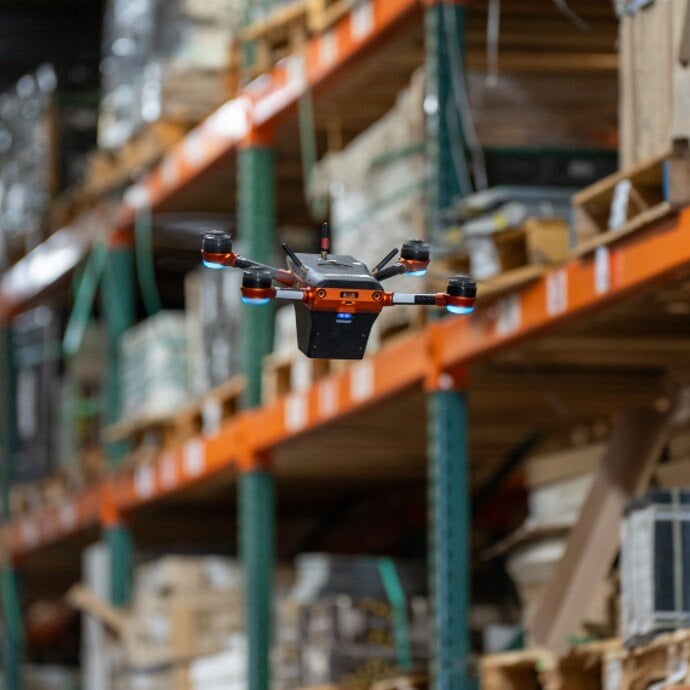
No modifications were made to MSI's existing infrastructure, including racking or labeling. Corvus One™ warehouse drones read any barcode symbology in any orientation placed anywhere on the front of cartons or pallets.
The Impact
-
Zero Operational Disruptions: Smooth integration with no interruptions to daily operations.
-
Enhanced Customer Satisfaction: Faster and more accurate order fulfillment.
-
Increased Labor Productivity: More efficient operations with actionable inventory data.
-
Prevention of Future Errors: Corrections made to workflows and processes to avoid repeat mistakes.
Where are we now?
After its first successful deployment in Southern California, MSI deployed Corvus One drones across its nationwide distribution network, including facilities in Washington, Arizona, Texas, Illinois, Georgia, Florida, and New Jersey.
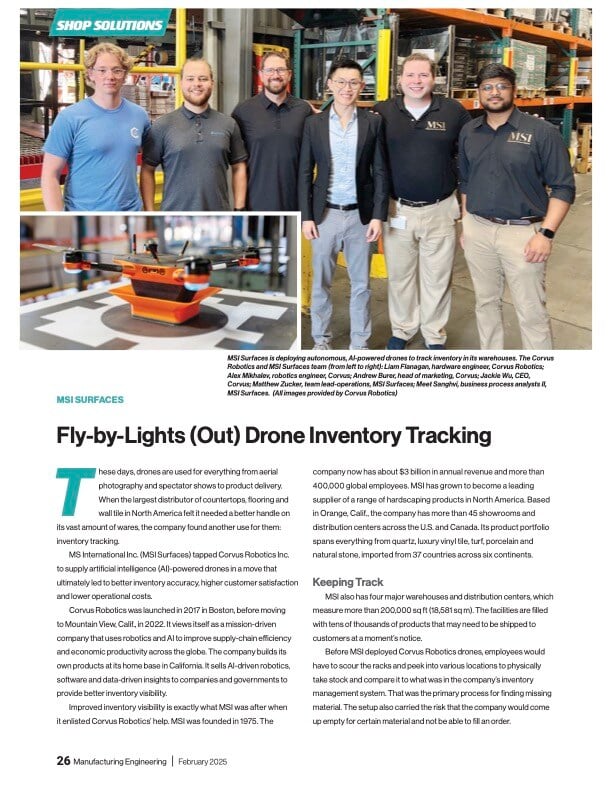
In the News
Fly-by-Lights (Out) Drone Inventory Tracking
Manufacturing Engineering Dive into a real-world case study with MSI Surfaces and see how Corvus One warehouse drones are delivering round-the-clock inventory visibility and helping streamline large-scale warehouse operations.
Drop Us a Line
Insights & Resources
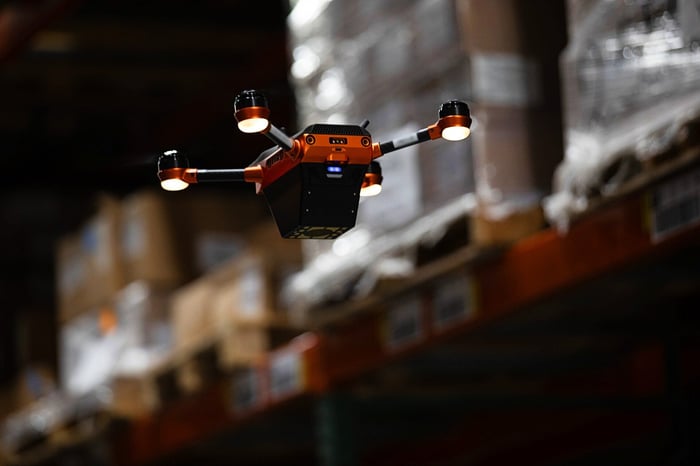
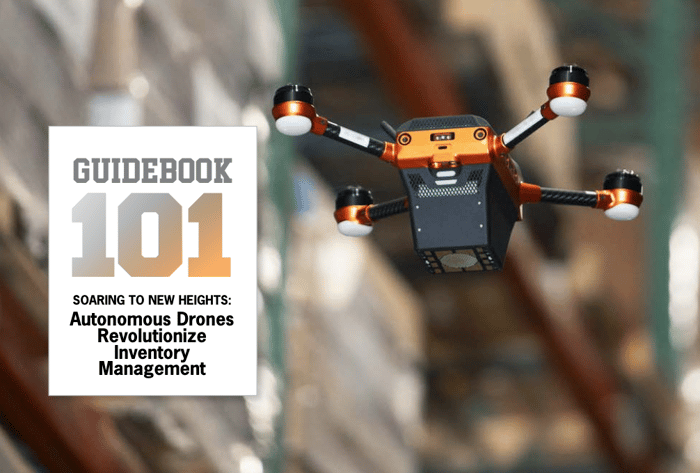
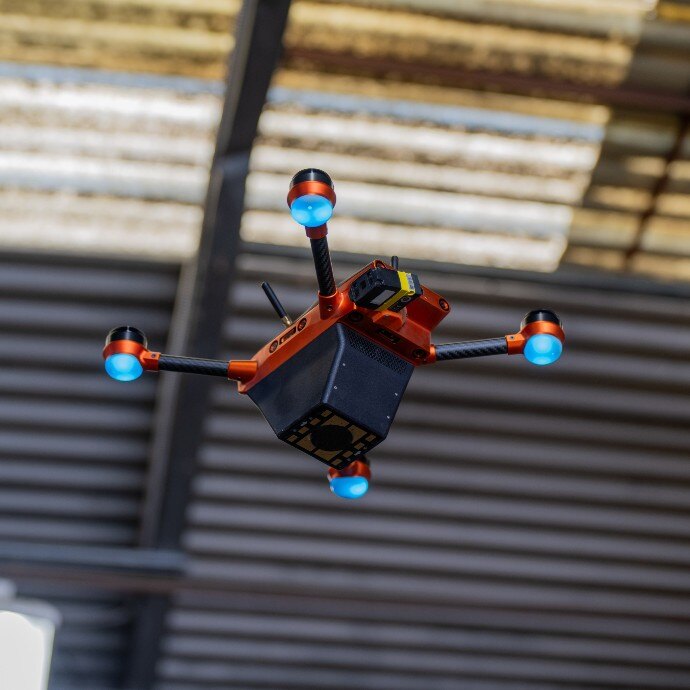
Press Release
Corvus Robotics Brings Autonomous Inventory Management System to Lights-Out Warehouses
Keep Reading